
The relation between the components (xi) forming the assembly (y) and the assembly itself can be a simple geometrical equation (like : y=x1+x2+x3-x4) as well as a non-linear complex function which cen be solved with FEM and/or CFD analyses.
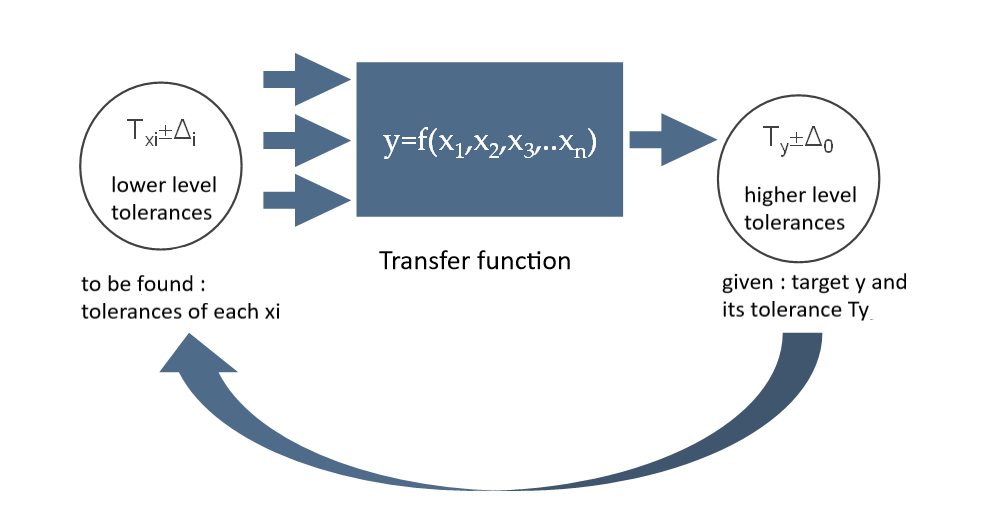
The cost plays an important role in the design of tolerances. The objective of an optimal tolerance design is to find an optimum strategy that results in minimum total cost and functional variability in production.
The calculation* of the tolerances of a system, starting from its components is “Tolerance Analysis” whereas the calculation of the tolerances of individual components starting from the tolerances of the system (assembly) is called “the distribution of tolerances” or “tolerance design”.
*The method of calculation may be “worst case analysis”, “statistical tolerancing” or “taguchi method”.
Statistical tolerance is based on the idea that it is very unlikely that the coincidental positive and negative deviations of the actual measurements of the individual parts from their respective nominal values are lined up in a most unfavorable case (for instance : the greatest possible positive dimensional deviations).
The assemblies having multiple parts are not destined to have large tolerances. Additionally maintaining narrow system tolerances is not costly.
Get your appointment for the one day lasting Tolerance Design and Statistical Tolerancing training soon.